Customer always ask why production take 23-30 days? Since our stress balls are out of stock in the US. Production will be started in our Chinese factory after order received.
This blog tells you why it takes so long and how necessary we need these days.
When it comes to manufacturing high-quality stress relievers, especially custom-designed ones, production is a complex process that takes time. The production time for stress balls typically ranges between 23 to 30 days, and many customers wonder why it takes so long. In this blog, we’ll dive into the key reasons behind this timeline and explain why this duration is crucial for ensuring the quality of your custom stress relievers.
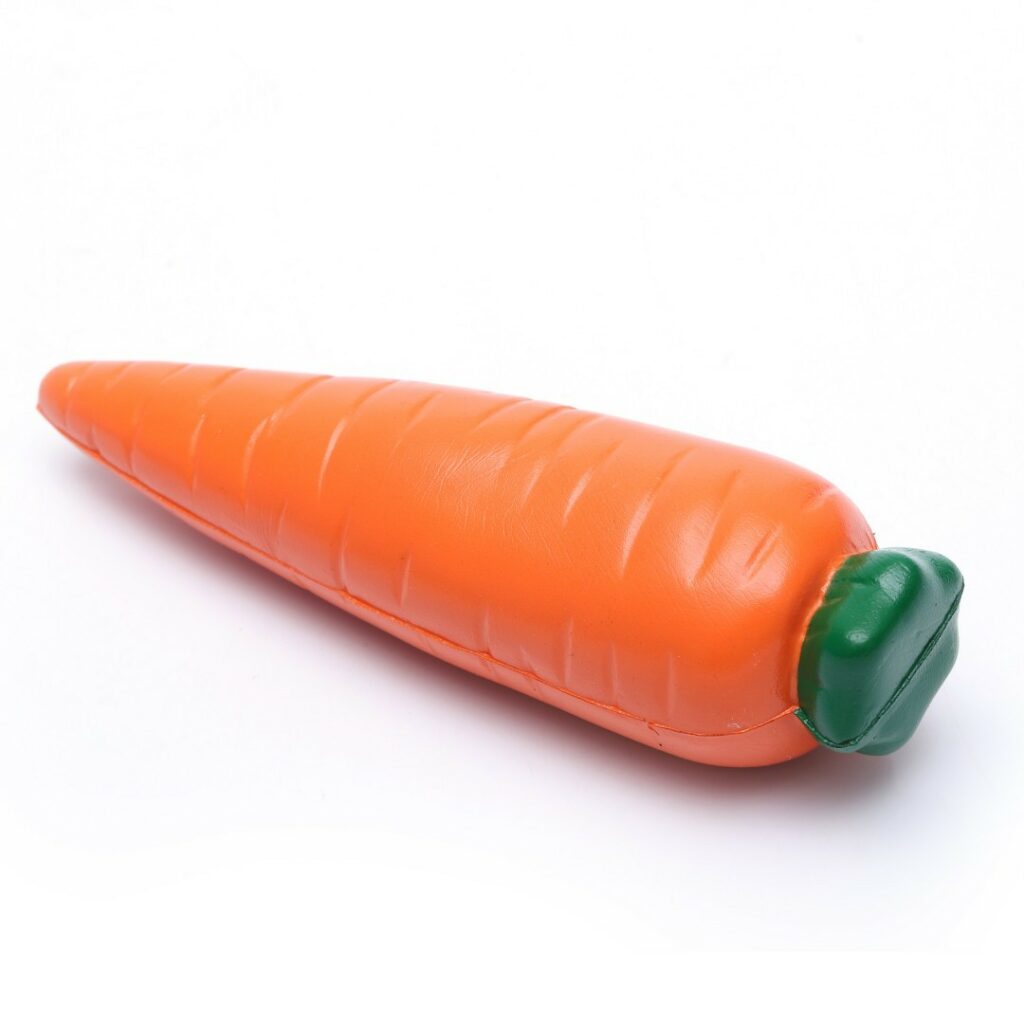
1. Material Preparation
The first step in producing stress balls is preparing the raw materials, which is a meticulous process that directly impacts the product’s quality. During this stage, each material, such as polyethylene or polypropylene, must be mixed in precise proportions with additives like foaming agents and flame retardants. Ensuring the right combination of materials guarantees the final product will have the desired softness, durability, and safety standards.
This initial step is critical, as any errors in the composition of the materials can lead to inconsistent quality or even product failure. Strict quality control is enforced at this stage, which contributes to the time required for the overall production.
2. Foam Molding Process
The heart of stress ball production lies in the foam molding process. Here’s an overview of the key steps involved:
- Material Mixing: The raw materials, including polyethylene and additives, are mixed according to a carefully controlled formula.
- Heating and Melting: The mixture is placed into a foaming machine, where it is heated until it melts into a moldable material.
- Foam Extrusion: This molten material is extruded into molds while injecting high-speed air to rapidly expand it into the desired ball shape.
- Cooling and Solidifying: The freshly molded stress balls are then cooled and hardened in specialized cooling systems, ensuring they retain their shape and texture.
This molding process is time-consuming due to the precision required at each step. The cooling phase alone takes considerable time to ensure the foam is fully solidified and doesn’t lose its shape.
3. Post-Production Treatment
Once the stress balls have been molded, they undergo several post-production treatments to enhance their quality and performance. These steps include:
- UV Protection Coating: For stress balls intended for outdoor use, a UV-resistant coating is applied to protect the material from sun damage and extend the product’s lifespan.
- Cutting and Shaping: After the molding process, the stress balls are cut and trimmed to meet the exact shape and size requirements specified in the design. This step ensures each stress ball is uniform in appearance and size.
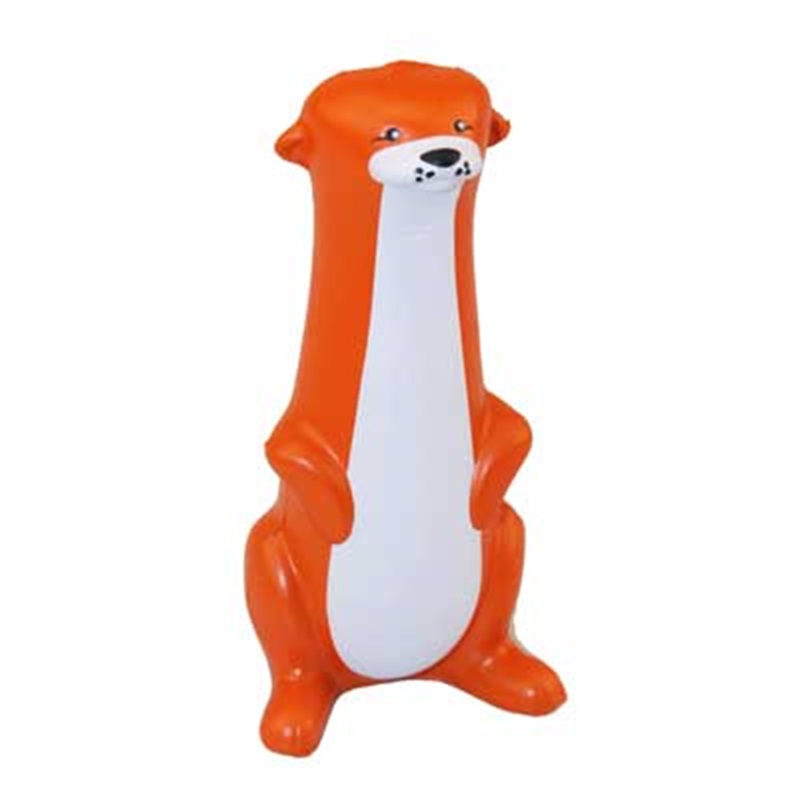
Printing Based on Customer Requirements
After the cutting and shaping process, the stress balls are printed with the customer’s logo or promotional message. This is a critical step that requires precision to ensure the logo is properly placed and adheres to the surface of the stress ball without compromising its texture or quality. At Novoline Promotions, we use advanced printing techniques to ensure your brand stands out clearly on every stress ball.
Quality Inspection
Every stress ball is inspected for defects or inconsistencies. The final products are thoroughly checked to meet industry standards and the customer’s specific design requirements.
Individual OPP Bag Packaging and Carton Boxing
Once the stress balls pass inspection, they are packed into individual OPP bags to protect them from damage during transport. After that, they are carefully placed in cartons, ready for shipment to ensure they arrive at your location in perfect condition.
Why Is This Timeline Important?
The stress relievers production time of 23 to 30 days may seem long, but this timeline is essential for delivering high-quality products that meet safety and durability standards. Rushing the process can lead to defects, improper molding, or substandard materials, all of which can affect the final product’s performance.
Consequences of Purchasing Low-Quality Stress Balls
Purchasing poor-quality stress balls can result in various issues, including:
- Premature Breakage: Stress balls made with subpar materials are more prone to cracking, tearing, or losing their shape quickly.
- Health Risks: If toxic materials are used, they can pose serious health risks to users, especially children or people with sensitivities.
- Negative Brand Impact: Poor-quality promotional stress balls can reflect badly on your brand, leaving customers with a negative impression.
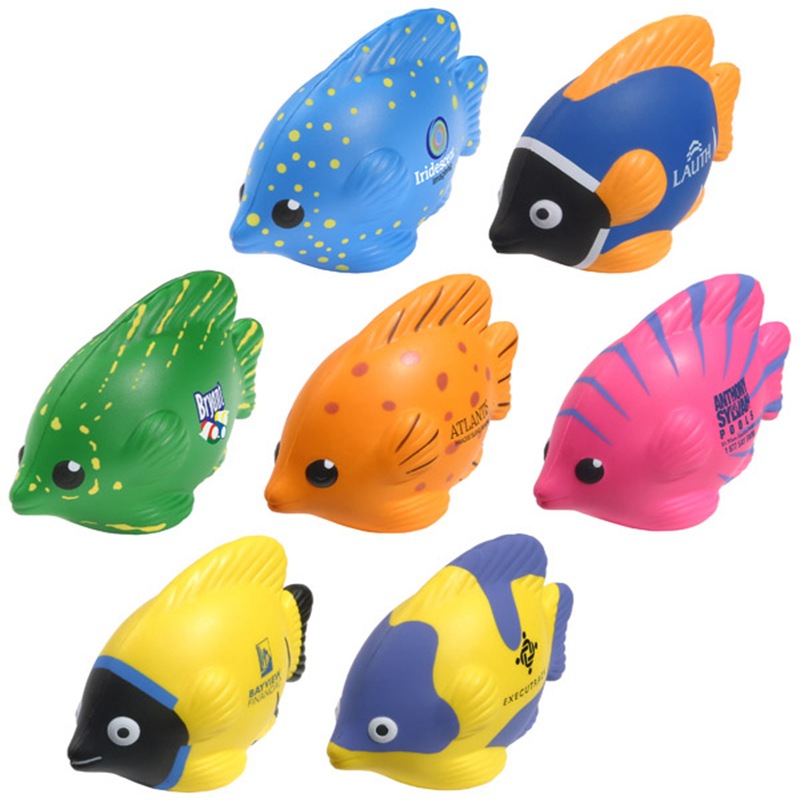
How to Ensure You Buy High-Quality Stress Balls
To avoid the pitfalls of low-quality stress balls, always choose a trusted manufacturer with a proven track record, like Novoline Promotions. Look for companies that follow a detailed production process, provide transparency, and offer customization options that align with your promotional goals.
At Novoline Promotions, we follow strict quality control procedures, use premium materials, and maintain high production standards to ensure your custom stress balls are produced with care. Our stress relievers production time reflects our commitment to quality, giving you the peace of mind that your promotional products will make a lasting impact.
Conclusion
The 23 to 30 days needed for stress relievers production isn’t just a random time frame—it’s essential for ensuring quality. With complex processes, from material preparation to post-production treatments, each step is crucial to delivering the best product possible. At Novoline Promotions, we take pride in our manufacturing process and are dedicated to providing you with high-quality, custom stress relievers that effectively promote your brand.
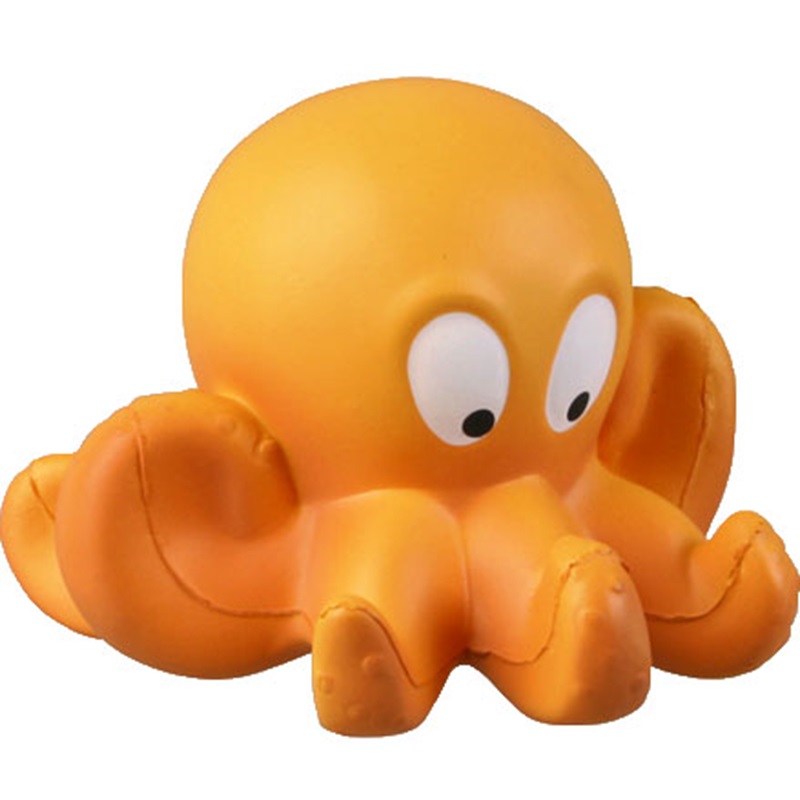